کوره ذوب کلیدیترین تجهیزاتی است که در فرایند تولید آهن آلات به کار میرود، چرا که تاثیر مستقیمی روی کیفیت محصولات نهایی خواهد گذاشت. ساخت مقاطع فولادی به روشهای گوناگونی امکانپذیر است؛ اما، استفاده از روش ذوب در کوره آهن آلات ارجحیت دارد. کوره ذوب انواع زیادی دارد که هر کدام مزایا و معایب مختص به خود را دارند و توسط شرکتهای مختلفی تولید میشوند. برای آشنایی با انواع این کورهها در ادامه با ما همراه باشید.
تعریف کوره
کوره ابزاری است که میتواند حرارت موردنیاز برای ذوب میزان مشخصی از آلیاژ را با سرعت و هزینهی قابل قبول ایجاد کند. کورهها انواع مختلفی دارند که با توجه به فاکتورهایی مثل هزینههای نصب، بهرهبرداری و نگهداری؛ کیفیت مواد خروجی، آلیاژ، میزان حرارت موردنیاز وغیره باید انتخاب شوند.
روش های تولید حرارت الکتریکی
در صنعت تولید آهن آلات انرژی الکتریکی را به روشهای مختلفی به سایر انواع انرژی تبدیل میکنند. کورههایی ذوبی که از این انرژی استفاده میکنند در انواع مختلف مقاومتی، القایی و قوس الکتریکی وجود دارند که در این مقاله با آنها آشنا خواهیم شد.
جهت آشنایی با کارخانه های تولید کننده شمش فولادی ایران مطلب زیر را بخوانید:
کارخانه های تولید کننده شمش فولادی در ایران
انواع کوره های صنعتی
کوره ذوب در انواع مختلفی در صنعت آهن آلات مورد استفاده قرار میگیرد که به بررسی مهمترین آنها در ادامه خواهیم پرداخت.
کوره بوتهای
از قدیمیترین و رایجترین کورههایی ذوب، کوره بوتهای است. هر چند امروزه با پیشرفت تکنولوژی و تجهیزات استفاده از این کوره رونق قبل را ندارد؛ ولی، همچنان در برخی از کارگاههای کوچک به عنوان کوره اصلی و در کارخانجات بزرگ به عنوان کوره آهن آلات کمکی مورداستفاده قرار میگیرد. در کورههای بوتهای برای ذوب کردن مواد از وسایلی به نام بوته استفاده میکنند و حرارت ایجاد شده به صورت غیرمستقیم و از طریق هدایت منجر به ذوب مواد درون آن خواهد شد.
کوره بوتهای خود انواع مختلفی چون: گرافیتی، سیلیکون کاربایدی و شاموتی دارد.
این کورهها از قسمتهای مختلفی مانند: بدنهای از جنس فلز نسوز، صفحه فلزی کف، دیواره ضدحرارت، درب، دستگاه ونتیلاتور، مشغل و زیر بوتهای تشکیل میشوند.
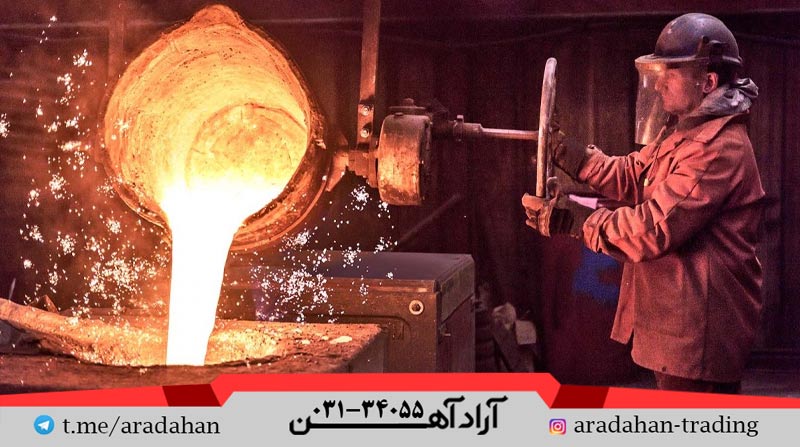
مزایا و معایب انواع کوره بوته ای
معایبی که میتوان برای کوره بوتهای برشمرد مواردی چون:
-هدررفت حرارتی بالا
-بازدهی و ظرفیت کم
– ایجاد آلودگی زیاد
– شارژ دستی
در مقابل این کوره آهن آلات از مزایای زیر برخوردار است:
- توانایی ذوب آلیاژها و فلزات مختلف
- هزینه نصب و بهره برداری پایین
- سهولت راهاندازی و استفاده
- هدررفت پایین عناصر
- تنوع در سوخت
- امکان تصفیه مستقیم مذاب در بوته
بوته گرافیتی
کوره بوته گرافیتی یکی از پرکاربردترین کورههای مصرفی در صنایع آهن آلات است که در انواع القایی، بوتهای و در شکلهای افقی یا عمودی مورد استفاده قرار میگیرد.
قیمت شمش فولادی کارخانه های معتبر کشور را در سایت آراد آهن مشاهده نمایید.
مزایا و معایب بوته گرافیتی
کوره بوته گرافیتی مزایای بسیاری دارد که عبارتند از:
- قابلیت تحمل و حفظ ساختار را تا حداکثر دمای ۳۵۰۰ درجه سانتیگراد دارد.
- حرارت ایجاد شده را به خوبی به دورن بوته اعمال میکند و تا جای ممکن مانع از هدررفت انرژی حرارتی خواهد شد.
- با مواد مذاب اولیه وارد واکنش شیمیایی نمیشود.
- قابلیت ذوب انواع مختلف فلزها و آلیاژها چون: آلومینیوم، مس، برنج، نقره و طلا را دارد.
- نسبت به ضربه مستحکم و مقاوم است.
تنها عیبی که برای کوره بوته گرافیتی میتوان برشمرد، حساسیت آن نسبت به اکسید شدن است. به همین منظور باید شرایطی چون عایقبندی کامل یا کنترل محیط با گاز خنثی برای استفاده از آن در نظر گرفته شود.
سیلیکون کاربایدی
کورههای بوتهای سیلیکون کاربایدی به منظور ذوب فلز و نگهداری مواد مذاب مورد استفاده قرار میگیرد. به منظور استفاده از این نوع کوره بوتهای باید نکات زیر را در نظر داشت:
- روکش داخلی و بیرونی بوته آسیبپذیر است و در هنگام جابهجایی و نصب باید به طور کامل محافظت شود.
- محیطی که برای نصب این کوره در نظر گرفته میشود، باید کاملا خشک باشد.
- بوته باید الزاما در وسط و مرکز کوره قرار گیرد.
- از آن جایی که احتمال انبساط در حین عملیات ذوب زیاد است، باید اطراف بوته فضای خالی وجود داشته باشد.
- حرارت باید به صورت غیرمستقیم به بوته برسد و نباید در تماس با کف یا دیوارهی آن باشد.
در صورتی که از کوره ذوب سیلیکون کاربایدی به منظور مذاب کردن استفاده میشود، باید ابتدا به مدت دو ساعت بوته در معرض دمای ۲۰۰ درجه سانتیگرادی قرار گیرد و پس از آماده سازی کامل بوته از میتوان با کمک حداکثر ظرفیت بوته به دمای ۹۵۰ سانتیگراد رسید. سپس مواد اولیه به منظور ذوب سازی به صورت پیوسته حرارت دهیخواهند شد.
اگر از کوره آهن آلات سیلیکون کاربایدی برای نگهداری مذاب استفاده شود. باید آماده سازی بوته با حرارت ۲۰۰ درجه و سپس رسیدن به ۹۵۰ درجه سانتیگراد مانند مراحل بالا صورت پذیرد و پس از آن به مدت یک ساعت بوته تحت دمای ثابت ۹۵۰ درجه قرار گرفته و بعد مورد استفاده قرار گیرد.
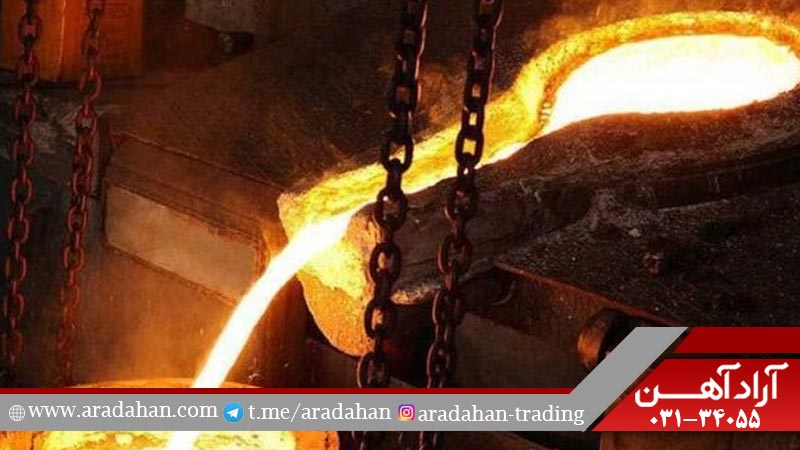
شاموتی
دلیل نامگذاری این کوره بوتهای استفاده از آجرهای مخصوصی به نام شاموتی در ساخت بدنهی آن است. این آجرها که از جنس اکسید سیلسیوم یا آلومینیوم هستند، مقاومت بالایی در برابر حرارتهای زیاد دارند و از آنها در صنایع دیگری چون شیشه سازی، ذوب فلزات غیرآهنی، ریختهگری فولاد و غیره نیز استفاده میشود.
بیشتر بخوانید: تفاوت آهن، فولاد و چدن در چیست؟
کورههای شعلهای
نوع دیگر کوره آهن آلات، شعلهای است که در شکلهای مکعب مستطیلی یا استوانهای ساخته میشود. این کوره در نوع چرخشی نیز تولید شده و و از آن تنها به منظور ریختگی چدن استفاده میکنند.
قدمت این کورهها که به نامهای دیگری چون تشعشعی یا روباده نیز شناخته میشوند به قرون وسطی برمیگردد. مهمترین ویژگیهای کورههای تشعشعی عبارتند از:
- موادی که برای مذاب شدن وارد کوره میشوند به صورت مستقیم با شعله و مواد آتشزا در تماس هستند.
- شارژ این کوره از طریق درب یا سقف آن امکان پذیر است.
- این کوره از گازوییل یا گاز طبیعی به عنوان سوخت استفاده میکند.
- ظرفیت این کوره بسیار متغیر و متنوع است. برای ذوب آلیاژهای غیر فلزی میتوان با حجمی بین ۱۵ تا ۷۵ تن از آن استفاده کرد و برای نگهداری مواد مذاب حتی تا ظرفیت ۹۰ تن هم قابلیت استفاده دارد.
مزایا و معایب انواع کوره شعله ای
- ساخت و نصب این کورهها آسان است و به هزینههای زیادی نیاز ندارد.
- سرعت ذوب کوره روباده بالا است.
- استفاده از ظرفیتهای متنوع و بالا برای ذوب توسط این کوره امکان پذیر است.
- – به طور کلی به دلیل محدودیت در ایجاد حرارت بازدهی پایینی دارد.
کوره کوپلا
به منظور ذوب چدن استفاده از کوره کوپلا نسبت به سایر کورهها ارجیحت دارد و به همین دلیل در بسیاری از کارگاهها و کارخانجات مورد استفاده قرار میگیرد.
این کوره به شکل استوانه تولید شده و قطر دیوارهی آن با توجه به سرعت و ظرفیت کوره تعیین میشود. ظرفیت کوره کوپلا نیز بسیار متنوع و بالا است و قادر است بین ۱۰ تا ۱۰۰ تن مواد را ذوب سازی کند.
کوره کوپلا از قسمتهایی چون ریل شارژ، پیش گرمکن هوا و تصفیه ساز گاز تشکیل شده است و موادی که درون آن قرار میگیرند، به صورت مستقیم با شعله در تماس قرار میگیرند.
مزایا و معایب انواع کوره کوپلا
از مزایای کوره کوپلا میتوان به مواردی چون ظرفیت مذاب سازی بسیار بالا و سهولت استفاده اشاره کرد. این کوره برای دستیابی به فوق گذارها محدودیت داشته و انعطاف لازم را ندارد که این تنها عیب آن محسوب میشود.
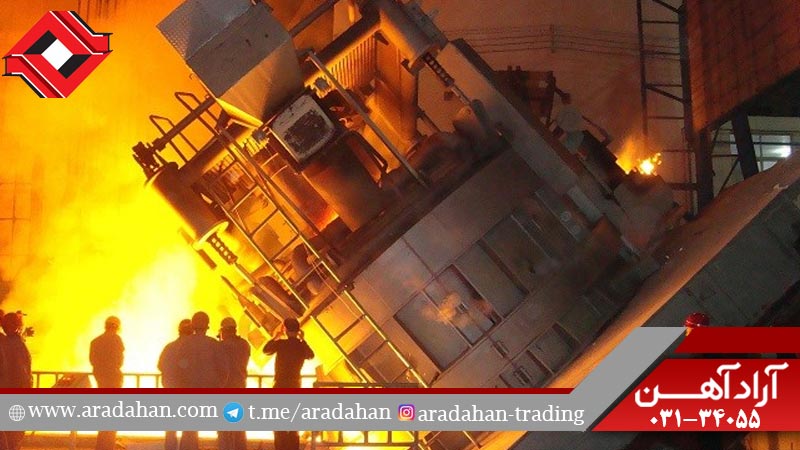
کوره مقاومتی الکتریکی
همان طور که از نام این نوع از کوره ذوب آهن برمیآید، انرژی لازم خود را برای رسیدن به دماهای بالا از طریق جریان الکتریکی با شدت بالا به دست میآورد. این جریان الکتریکی از مقاومتها عبور کرده و باعث افزایش دمای کوره خواهد شد. مقاومتهایی که در ساخت این کوره مورد استفاده قرار میگیرند، از متریالی مقاومی تولید میشوند تا در برابر حرارت بالا، خوردگی و اکسیداسیون محیط کوره در امان باشند.
کورههای مقاومتی در انواع زیر وجود دارند:
- گرم کننده مستقیم: در این نوع کوره ولتاژ الکتریکی کم اما شدت جریان آن زیاد است و به صورت مستقیم به شارژ متصل میشود. این کوره به منظور حفظ گرما و ذوب مورد استفاده قرار میگیرد.
- گرم کننده غیرمستقیم: در این نوع کوره جریان برق از طریق عبور از مقاومتهایی که اطراف کوره قرار گرفتهاند، حرارت لازم را در بوته ایجاد میکنند. سپس حرارت ایجاد شده از طریق بوته به شارژ رسیده و باعث ذوب مواد خواهد شد.
مزایا و معایب انواع کوره مقاومتی الکتریکی
از مزایای کوره مقاومتی میتوان به قابلیت کنترل ترکیب شیمیایی مواد مذاب اشاره کرد.
بالا بودن قیمت انرژی برق و سایر هزینههای کوره مقاومتی کنار ظرفیت پایین آن از جمله معایب این کوره به شمار میروند. شایان ذکر است که حداکثر ظرفیت این کوره ذوب تنها ۵۰۰ کیلوگرم است.
جهت اطلاع از قیمت آهن آلات برروی لینک زیر کلیک کنید:
قیمت روز آهن آلات ساختمانی و صنعتی
کوره القایی
جدیدترین کوره آهن آلات با استفاده از میدان مغناطیسی عملیات ذوب مواد را انجام میدهد. در کوره القایی با کمک فلز رسانایی که درون یک سیم پیچ تعبیه شده و عبور دادن جریان الکتریکی از درون آن یک میدان مغناطیسی در مخزنی که مواد درون آن قرار میگیرند، ایجاد میشود که تغییر جریان ورودی با سرعت زیاد موجب ایجاد حرارت و تغییر در ساختار مولکولی فلز و تبدیل آن به مایع خواهد شد.
کورههای القایی براساس فرکانس تولید در سه دستۀ:
فرکانس پایین با تنها ۵۰ هرتز
فرکانس متوسط ۲۰۰ تا ۱۰۰۰ هرتز
و فرکانس بالا با بیش از ۱۰۰۰ هرتز
تقسیمبندی میشوند.
کورههای فرکانس پایین بازدهی کمی دارند و در اغلب موارد قدرت لازم برای مذاب کردن مواد را ندارند. به همین دلیل در بیشتر مواقع از آنها در آزمایشگاهها استفاده میشود.
مزایا و معایب انواع کوره القایی
- ایجاد و پخش حرارت کافی
- امکان کنترل ترکیب شیمیایی
- امکان افزایش دما تا مقدار بسیار بالا
- میزان مصرف انرژی کمتر نسبت به کوره مقاومتی
- عدم امکان تصفیه مذاب
مصرف جریان برق و هزینههای مربوط به آن در این کوره گرچه نسبت به کوره مقاومتی کمتر است، اما در نوع خود قابل توجه است.
بیشتر بخوانید: نرماله کردن فولاد به چه معناست؟
کوره قوس الکتریکی
در این کورهها توسط قوس الکتریکی حرارت مورد نیاز ایجاد میشود و به دو صورت مستقیم یا غیر مستقیم به مواد انتقال مییابد.
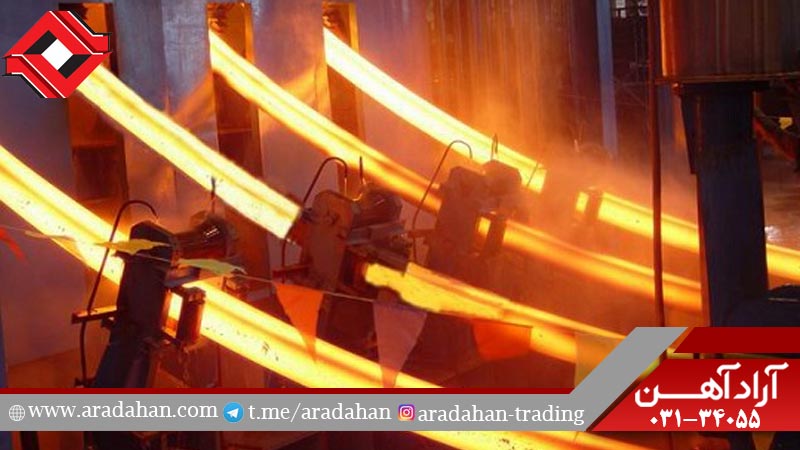
مزایا و معایب انواع کوره قوس الکتریکی
مزایای این کوره شامل:
- امکان استفاده از قراضههای ارزان قیمت
- ایجاد دمای بالاتری در مقایسه با کوره القایی
- عدم نیاز به تمیز بودن کوره
- میزان مصرف کمتر انرژی در مقایسه با کوره القایی
میشود و بزرگترین عیب آن بالا بودن هزینههای گرافیت و مواد نسوز به کار رفته در کوره است.
جمع بندی
کوره ذوب آهن یکی از مهمترین تجهیزاتی است که در صنعت آهن آلات مورد استفاده قرار میگیرد و نوع آن با کیفیت مواد خروجی رابطهی مستقیمی دارد. کورههای ذوب در انواع بسیار مختلفی وجود دارند که هر کدام دارای معایب و مزایای هستند. در این مقاله به بررسی مهمترین کورهها و مزایا و معایب هر کدام از آنها پرداختیم.